Daimec, a leading bathroom furnishings company, stands out for its wide range of services that include galvanic treatments, vanishing and PVD. However, it is in the processing of zamak, a fine alloy of zinc and aluminum, that the company excels, thanks to the presence of an in-house die casting foundry.
The quality of the workmanship is a key aspect for Daimec, which follows every stage of the production process from start to finish, starting with the creation of the products.
The company pays great attention to ensuring defect-free molding, which is essential to avoid complications in subsequent stages. To this end, continuous inspections are carried out, strictly adhering to the specifications of the control sheets drawn up by the technical department.
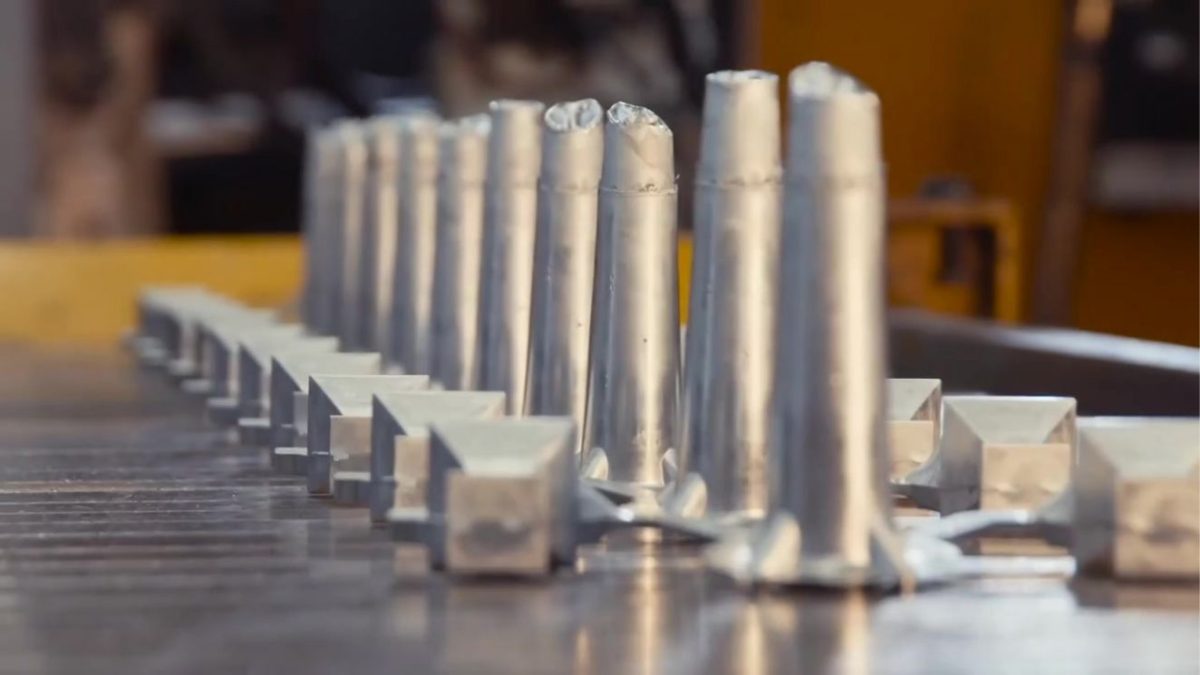
Any dimensional or aesthetic problems are detected promptly, allowing immediate corrections. The cleaning department adjacent to the foundry is equipped with advanced technologies to perform surface polishing and correct defects such as porosity and heat lines. In addition, the parameters of the die casting machine can be adjusted to further optimize the quality of the parts.
Other secrets to success: quality of raw materials and certifications
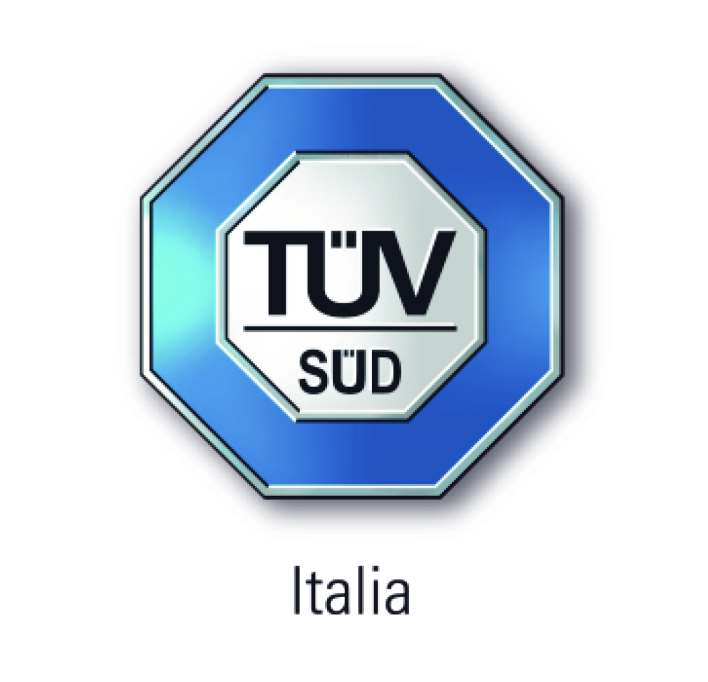
Daimec emphasizes the use of certified raw materials, supplied with accurate documentation regarding origin and composition. Zamak 15 is often the first choice to meet the company’s production needs.
The quality of production processes is guaranteed by the ISO 9001-compliant control system, to which Daimec is certified. An ongoing commitment to quality excellence that has established Daimec’s reputation as a benchmark in the aesthetic materials processing industry, providing customers with impeccable and reliable results.
To learn more, visit the website!